Canadian Warranty Repair Depot for Global Electronics Brands
Cut RMA turnaround to 2 days* while keeping every unit—and every customer—inside Canada.
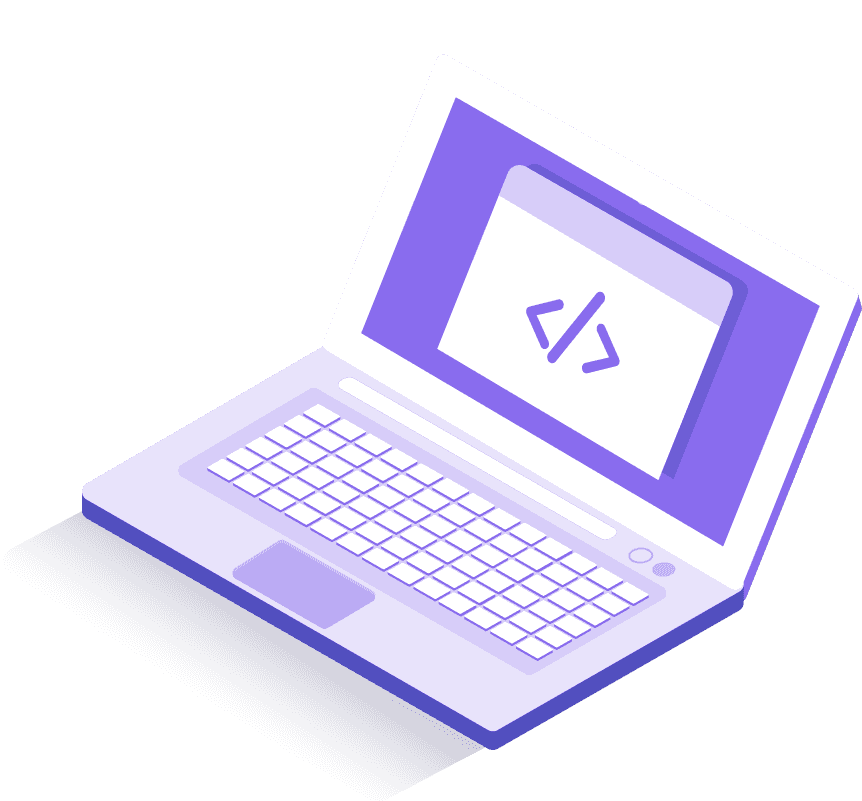
Key Takeaways
Why Manufacturers Choose Microland
For more than three decades, tier‑1 electronics brands have relied on Microland to safeguard their reputation in Canada. Our repair labs marry board‑level craftsmanship with proprietary, AI‑driven workflow software, yielding a 97 percent first‑time‑yield and real‑time visibility from check‑in to ship‑out. With bilingual support, API integrations, and <40‑hour triage, we turn warranty headaches into five‑star customer experiences—and give your ops team the data to prove it.
Proven & Trusted
By some of the top global electronics brands in the world like Sony and Yamaha.
AI Enabled Software-First Approach
From receiving to shipping, repair to parts management, our system are custom design and built in-house with automation, integration and AI woven into the DNA of our service approach
Expertise
From board swapping down to component level BGA repair and rework with advanced diagnostic and analysis tools
30 Years
Repairing A/V, Computing, POS and Mobile products for tier-1 OEMs in Canada
Prime Location
Located in the Greater Toronto Area, we offer a prime location for cost effective shipping and walk-ins
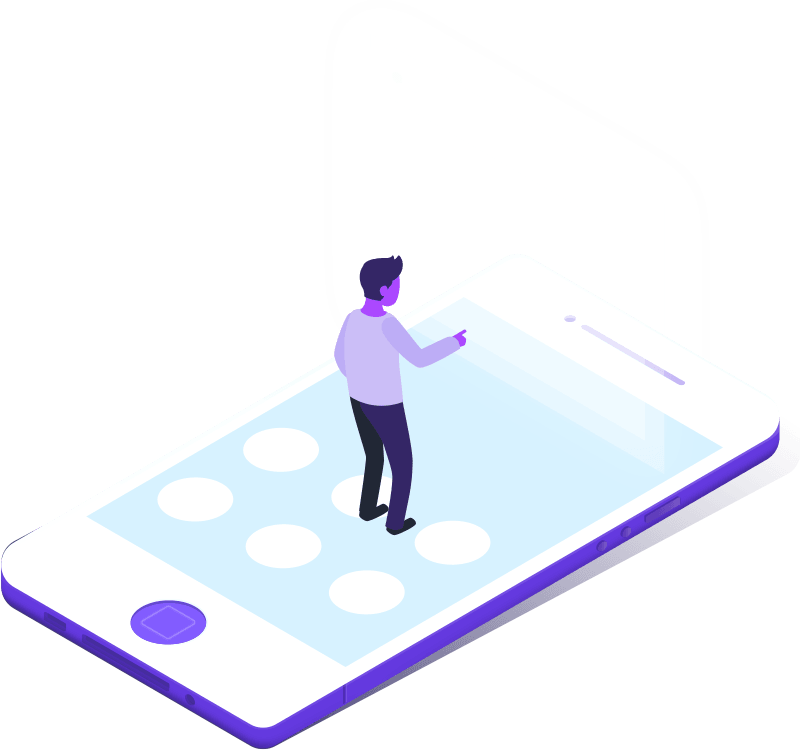
Why Canada Matters
Shipping warranty units south of the border can add 10-14 days, brokerage fees and return‑to‑Canada duties.
By handling service at our Markham depot you:
- Eliminate cross‑border delays and tariffs under USMCA.
- Give Canadian customers a simple domestic return label.
- Maintain bilingual (EN/FR) paperwork and support.
- Leverage same‑day GTA courier and next‑day ground to QC & Atlantic Canada.

Our end-to-end workflow
Our 7‑Step Depot Process
- Receive & log – Barcode scan, HD photos and serial validation at the dock.
- Triage – Technician diagnosis against OEM rules; core failures coded for analytics.
- Quote & approval – API or portal push; your team signs off in one click.
- Repair / refurbish – Board‑level, component-level, cosmetic and firmware updates.
- QC & burn‑in – Automated scripts; results stored for 7 years.
- Pack & ship – ISTA‑approved packaging and tracking back to channel or end user.
- Reporting – Daily KPI file plus monthly Pareto & corrective‑action review. API integration.
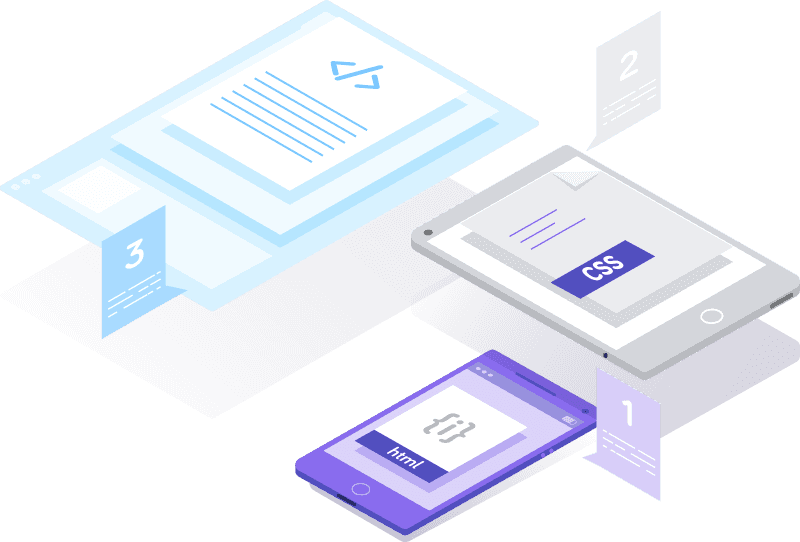
Proven Results – Case Study
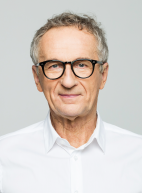
Vice President of Business Development, Global Consumer Electronics OEM
Get a copy of our latest Case Study on an ongoing nationwide, high volume, warranty project
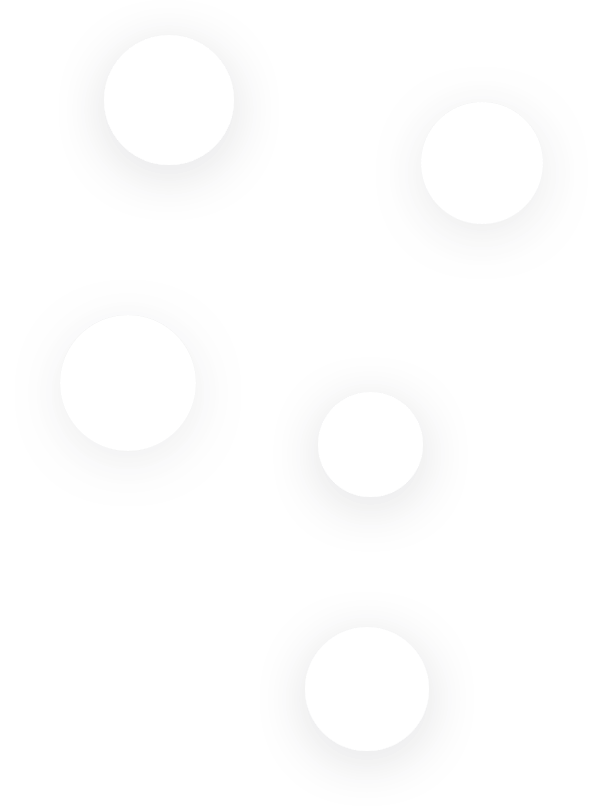
FAQ
Frequently asked by OEM service teams
The questions below come up on nearly every discovery call with service, operations and logistics leaders. If yours isn’t answered here, reach out—we’ll turn it around as quickly as we do our repairs.
What turnaround time can I expect?
With parts in stock, you can expect 2 day repair TATs.
What data‑security standards do you follow?
ISO 27001‑aligned processes with NIST 800‑88 drive‑wipe or physical shredding as required.
Can you handle bilingual customer service?
Absolutely. Our portal, phone and email support are available in English and French.
How will you share data with us?
We can integrate with your APIs to push data into your systems. We also have our own APIs so you can pull data from ours.
Ready to get started?
Get in touch